近年来,风力发电作为新兴能源之一,凭借其自身在降低环境污染及解决偏远地区居民用电难等问题上的突出表现,在世界各国的能源结构中逐步占据了至关重要的地位。统计结果显示,截至2012 年底,全国风电累计核准容量10670万kW,并网6266万kW,在建4404万kW, 2012年上网电量1008亿kW_h,全国风电累计装机占全球市场23%,位列世界第一。风力发电是“十二五”规划中国家重点能源发展方向,风机主轴作为风力发电机内的核心部件,具有形状复杂,锻造难度大等特点,大锻件结合45000kN水压机锻造能力,通过使用专用漏盘,配合合理的锻造工艺,成功地解决了法兰成形、圆角成形、轴身同轴度等锻造难题,并节约了成本,缩短了生产周期,使企业具备了规模生产 1.5 ~ 3MW风机主轴锻件的能力。
原风机主轴锻造工艺及存在问题
风机主轴锻件作为典型的大型异型件:端部法兰与轴身直径差最大可达lm以上,同轴度不易保证,锻件成形后校直困难,连接部位圆角很大,且端部法兰锻造比要求高,传统镦粗-拔长工艺不能满足生产要求,受到锻压设备的限制,工艺上存在局限性。
原锻造工艺共分为四火,第一火压钳把、压圆,第二火镦粗、拔长、下料,第三火将轴身部分
放入漏盘内,用平砧旋转辗压成形法兰,最后一火将轴身部分拔长成形。以1.5MW风机主轴为例,存在问题主要包括:
(1)由于法兰与轴身直径差大,为保证锻件同轴度,同时为了防止法兰边缘出现缺肉,采取增加法兰厚度的方法,法兰下料重量达到3.7t。
(2)法兰与轴身连接处圆角角度大,直接锻造困难,采用添加锻造余块增大轴身直径,后续机加工成形的方法,下料重量达到2.2t。
(3)为满足法兰端锻造比要求,必须采用平砧旋转辗压镦粗成形的锻造工艺方法,但是由于水压机车间现有45 OOOkN水压机活动横梁与移动工作台净空距仅为4.5m,上平砧髙度约1.1m,而1.5MW、2MW风机轴锻件带钳把长度均达到4.5m 左右,3MW风机轴锻件长度更达到5m左右,无法 一次拔长至锻件尺寸,所以轴身部分必须分为两次拔长成形,增加锻造复杂程度。
(4)由于冒口端烂料是在成形后锯掉,很有可能出现由于法兰端下料过大,为保证锻件长度而将冒口端烂料带入锻件,影响锻件质量的情况。
针对上述问题,我公司结合实践设计了所示的新型漏盘,该漏盘在具备原漏盘所有优点的基础上,更具有便于修整法兰直径,法兰成形效果好,漏盘胀形力小,使用寿命长、便于脱模等优点。为采用新漏盘锻造成形的1.5MW风机主轴。针对水压机净空距小,锻件轴身需两次拔长成形及冒口端烂料带入锻件的问题,采用第二火镦粗拔长后上锭身重新压钳把,将冒口端烂料剁掉,把锻件最后一个台阶作为钳把的方法,将轴身部分的两次拔长工序缩短为一次拔长成形,节省一个锻造火次。
改进后的新锻造工艺仅三火:第一火压钳把、倒棱、错底;第二火镦粗压方重新压钳把,下料; 第三火漏盘内辗压法兰成形,修整锻件。通过在生产实践中不断探索,我公司已经掌握 了 1.5 ~3MW风机主轴锻件生产的核心技术,采用新锻造工艺后各级别风机主轴使用的钢锭均比原来减重3~4t,钢锭利用率提高,极大程度降低了生 产成本。同时提髙了产品外观及内部质量,缩短近50%生产周期,现巳具备年产上千支风机主轴的能力,为企业在市场竞争中立于不败之地打下坚实基础.
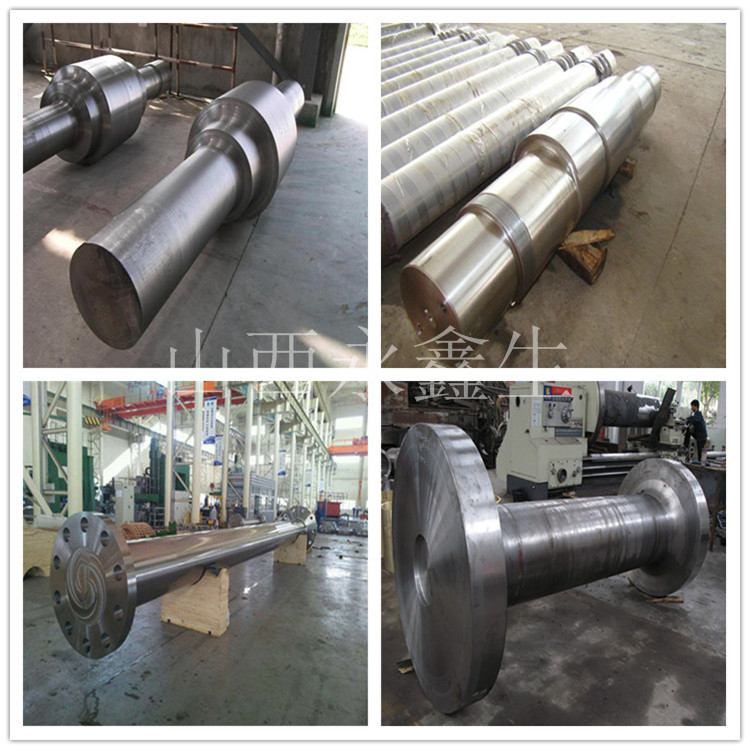